Podkład podłogowy pełni ważną funkcję w konstrukcji podłogi. Od tego, czy jest równy i wytrzymały zależeć będzie trwałość układanego na nim materiału posadzkowego. Odpowiednie wykonanie podkładu pozwoli zapobiec uszkodzeniom posadzki w przyszłości – odspajaniu się elementów drewnianych, pękaniu płytek czy wypaczaniu paneli.
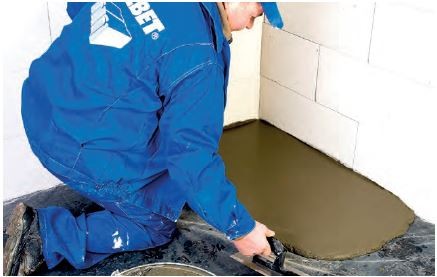
Istotną rolę w budynku odgrywają przegrody
poziome. W nich z kolei ważne są
poszczególne warstwy. Jedną z nich jest
podkład podłogowy, który stanowi ostatnią
warstwę podłogi przed wykonaniem
posadzki. Jest on niezbędny pod materiałami
podłogowymi, takimi jak np. płytki,
parkiet, panele czy wykładziny. Podkłady
podłogowe popularnie nazywa się
jastrychem, wylewkami lub szlichtami.
Wykonuje się je najczęściej na mokro, są
to wówczas wylewki cementowe lub anhydrytowe.
Podkłady występują również
w postaci suchych jastrychów.
Zadaniem podkładu podłogowego jest
przenoszenie obciążeń użytkowych podłogi
na podłoże, jeżeli materiał podłogowy
nie może spełnić tego zadania samodzielnie. Od dobrego podkładu oczekuje
się, by był mocny, odporny na obciążenia
występujące w czasie użytkowania podłogi,
równy, bez spękań oraz odpowiednio
suchy. Niekiedy podkład podłogowy
musi posiadać dodatkowe, specjalne cechy,
np. przy ogrzewaniu podłogowym
powinien dobrze przewodzić ciepło i być
odporny na duże wahania temperatury.
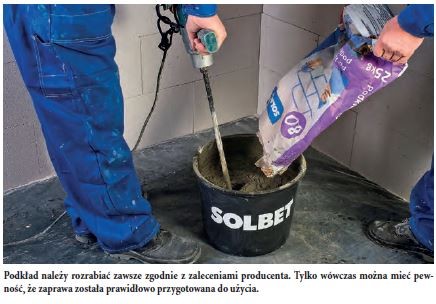
Podkłady z suchej mieszanki
Podkłady podłogowe SOLBET to produkty na bazie spoiwa cementowego. Mają postać fabrycznie przygotowanej suchej mieszanki cementu, wyselekcjonowanych kruszyw mineralnych oraz domieszek poprawiających parametry techniczne i właściwości robocze. Stanowią one dobrą alternatywę dla tradycyjnych jastrychów cementowych przygotowywanych na budowie. Ich zastosowanie znacznie ułatwia i przyspiesza wykonanie prac. Przygotowanie podkładu podłogowego z gotowej mieszanki zajmuje mniej czasu niż podkładu rozrabianego na budowie z poszczególnych produktów. Gotowe mieszanki wystarczy jedynie rozrobić z odpowiednią, wskazaną na opakowaniu ilością wody, by produkt był gotowy do użycia. Stosowanie podkładów w postaci suchej mieszanki zapewnia również wysoką jakość otrzymanego produktu. Mniejsze jest też ryzyko popełnienia błędu przy rozrabianiu zaprawy, ponieważ nie wymaga precyzyjnego dozowania kilku składników – potrzebna jest jedynie odpowiednia ilość wody.
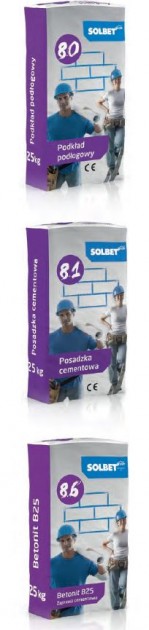
Rodzaje podkładów podłogowych Podkłady podłogowe z uwagi na układ konstrukcyjny można podzielić na związane (zespolone) lub niezwiązane z podłożem (np. pływające).
Podkłady zespolone z konstrukcją
wykonuje się bezpośrednio na elemencie
konstrukcyjnym, np. stropie lub betonowej
płycie na gruncie. Układ taki,
jak sama nazwa wskazuje, pozbawiony
jest jakiejkolwiek warstwy oddzielającej
(izolacji przeciwwilgociowej, termicznej
czy akustycznej). Podkład i element konstrukcyjny
współpracują, jakby tworzyły
całość.
Gdy powierzchnia konstrukcji jest słaba,
bardzo chłonna, wilgotna czy zaoliwiona,
aby prawidłowo wykonać wszystkie
warstwy podłogi pod jastrychem należy
wykonać warstwę oddzielającą – izolację
przeciwwilgociową z folii, przeciw wodnej
z papy lub innej warstwy zapewniającej
możliwość przesunięcia się podkładu
po podłożu. Izolację układa się szczelnie
(z zakładem), bez fałd i wywija ją na ściany.
Taki podkład na warstwie oddzielającej
bardzo dobrze przekazuje na podłoże
obciążenia pionowe przy możliwym
przesuwaniu się poziomym.
Najczęściej stosowanym rodzajem podkładu jest tzw. podkład pływający. Układa się go na warstwie izolacji termicznej lub akustycznej. Może być ona wykonana z twardej wełny mineralnej lub elastycznego styropianu. Na takiej izolacji układa się szczelną izolację przeciwwilgociową lub przeciwwodną, a następnie warstwę jastrychu.
Stosując produkty SOLBET można wykonać wszystkie te rodzaje podkładów.
Zastosowanie podkładów SOLBET
Do wykonywania jastrychów wewnątrz budynku przeznaczony jest Podkład podłogowy 8.0. Może być on stosowany podczas wykonywania podkładów zespolonych z podłożem na spoiwach hydraulicznych oraz do wykonywania podkładów na warstwie rozdzielającej, tzw. „pływających”, na warstwie paroizolacyjnej lub przeciwwilgociowej. Podkład podłogowy 8.0 sprawdzi się zarówno w suchych, jak i wilgotnych pomieszczeniach. Został on zaprojektowany z myślą o układaniu mechanicznym za pomocą mixokreta.
Do wykonywania jastrychów na zewnątrz, jak i wewnątrz budynku służą dwa produkty SOLBET : Posadzka cementowa 8.1 oraz zaprawa cementowa Betonit B25 8.6. Oba produkty nadają się do wykonywania podkładów podłóg ogrzewanych oraz podkładów niezwiązanych z podłożem. Ze względu na wysoką wytrzymałość są odpowiednie do stosowania zarówno w budynkach mieszkalnych, jak i przemysłowych czy magazynach, na podjazdach, tarasach itp. Produkty te przeznaczone są do układania ręcznego lub mechanicznego za pomocą mixokreta. Ponadto Posadzka cementowa 8.1 charakteryzuje się wysoką odpornością na ścieranie, dzięki czemu może stanowić warstwę ostateczną. Z kolei Betonit B25 jest produktem o szerszym zastosowaniu. Może być również używany do napraw betonu i prac betoniarskich takich, jak sporządzanie czap kominowych, słupków ogrodzeniowych oraz nadproży okiennych i drzwiowych.
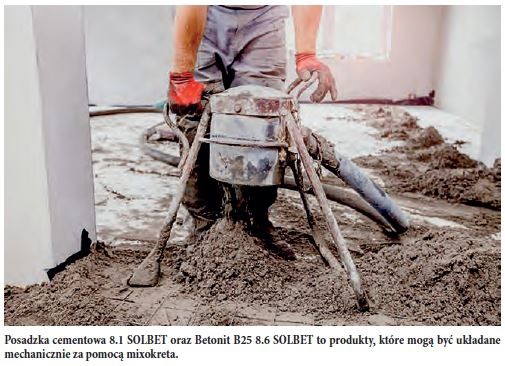
Prace przygotowawcze
Warunkiem prawidłowego wykonania podkładu podłogowego jest staranne przygotowanie podłoża, na którym będzie on wykonywany. Podkład podłogowy można aplikować na wszystkie mocne i nośne podłoża cementowe. Powinny być one oczyszczone z substancji obniżających w znacznym stopniu przyczepność, takich jak tłuszcze, bitumy i pyły. Luźne elementy oraz fragmenty podłoża o słabej wytrzymałości należy usunąć mechanicznie, np. skuć. Jeżeli istnieje potrzeba zredukowania chłonności podłoża, należy zastosować Grunt Akrylowy Głębokopenetrujący 9.7 SOLBET jedno- lub dwuwarstwowo. Drugą warstwę emulsji nanosi się poprzecznie do pierwszej, po upływie ok. 2 godzin, nie pozostawiając kałuż. Do nakładania zaprawy można przystąpić po wyschnięciu emulsji gruntującej. W przypadku wykonywania podkładu na warstwie oddzielającej lub w układzie tzw. pływającym należy zadbać o dokładne i równe rozłożenie na podłożu wszystkich warstw izolacji termicznej bądź akustycznej. Ściany i inne elementy występujące w polu wykonywanych prac powinny być oddzielone (dylatowane) od przyszłej posadzki.
Wymagane dylatacje
Cementowe podkłady podłogowe podlegają
skurczowi, co może powodować
pęknięcia ich powierzchni. Konieczne
jest więc wykonanie dylatacji. Wykonując
podkład z zastosowaniem gotowych
mieszanek należy zawsze zapoznać się
z zaleceniami producenta dotyczącymi
wykonywania dylatacji.
Dylatacje obwodowe wykonuje się wzdłuż
pionowych elementów konstrukcyjnych
budynku – ścian oraz słupów. Podkład
posadzkowy powinien być oddzielony od
nich paskiem papy lub paskiem izolacyjnym,
mocowanym punktowo.
By posadzka nie popękała w przypadkowych
miejscach, na dużych płaszczyznach
oraz w przejściach między pomieszczeniami
należy wykonać dylatacje
pośrednie. Są to nacięcia o głębokości
1/3–1/2 grubości podkładu z podziałem na
pola o długości boku nie większym niż
6 m. Czynność ta powinna wymusić powstanie
pęknięć w miejscu nacięcia.
Ponadto w miejscu łączenia dwóch powierzchni
nieogrzewanej i ogrzewanej
czyli podkładzie na ogrzewaniu podłogowym
wykonuje się tzw. dylatacje rozdzielcze.
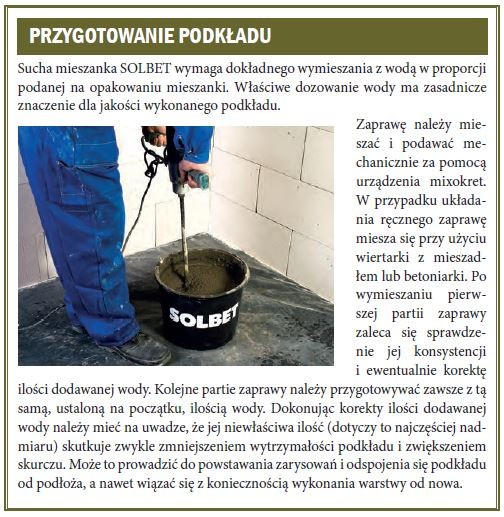
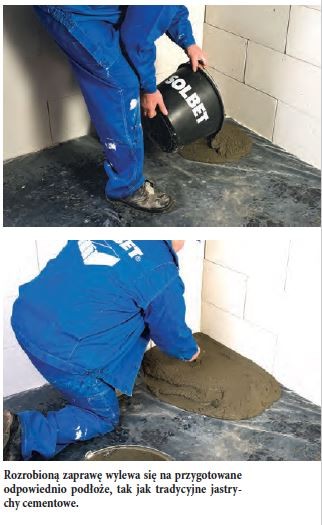
Wykonanie podkładu
Rozrobioną zaprawę wylewa się na przygotowane
odpowiednio podłoże, tak jak
tradycyjne jastrychy cementowe. Grubość
warstwy odmierza się wypoziomowanymi
prowadnicami, po których
rozprowadza się zaprawę przy pomocy
drewnianej lub metalowej łaty. Po usunięciu
prowadnic miejsca po nich należy
skropić wodą, wypełnić zaprawą i wygładzić
stalową pacą. Kolejne porcje zaprawy
zaleca się układać możliwie szybko, tak
aby mogły połączyć się przed rozpoczęciem
wiązania. Całą powierzchnię należy
zatrzeć na gładko. Szerokość układanego
pola nie powinna przekraczać 2 m. Przerwy dylatacyjne powinny zostać wykonane
zgodnie z technologią wylewania podkładów
i posadzek cementowych.
Jastrychy cementowe wymagają odpowiedniej
pielęgnacji, czyli ochrony przed
zbyt szybką utratą wilgoci w trakcie prac
i w pierwszym okresie po ich zakończeniu.
Wykonaną powierzchnię należy
chronić przed zbyt szybkim wysychaniem,
bezpośrednim nasłonecznieniem,
niską wilgotnością powietrza lub przeciągami.
W celu zapewnienia dogodnych
warunków wiązania zaprawy, w zależności
od potrzeb, świeżo wykonaną
powierzchnię można zraszać wodą lub
przykrywać folią. Należy również ograniczyć
ogrzewanie pomieszczenia, w którym
wykonano wylewkę.
Zaniedbanie zabiegów pielęgnacyjnych
może skutkować większym skurczem,
który spowoduje m.in. pojawienie się
spękań.
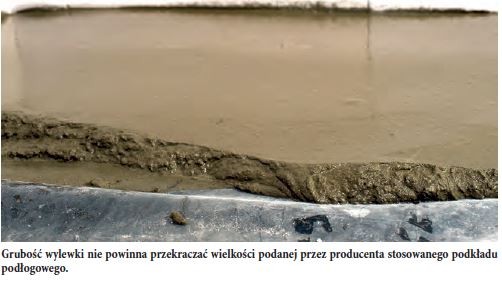
Czas wysychania wylewki cementowej
zależy od grubości warstwy oraz warunków
termiczno-wilgotnościowych panujących
w otoczeniu.
Dane techniczne i informacje o sposobie
stosowania podkładów SOLBET dotyczą wykonywania prac w temperaturze
20±2°C i wilgotności względnej 65±5%.
W innych warunkach należy uwzględnić
szybsze lub wolniejsze twardnienie materiału.
Ważne zalecenia
Grubość wylewki podłogowej zwykle jest uwzględniona
w projekcie. Powinna być uzależniona od rodzaju konstrukcji
podłogi oraz stopnia ściśliwości warstwy izolacji cieplnej lub
przeciwdźwiękowej.
Minimalna grubość warstwy Podkładu podłogowego 8.0
SOLBET powinna wynosić 25 mm w przypadku podkładu
związanego z podłożem i 35 mm w przypadku podkładu
wykonywanego na warstwie rozdzielającej. Maksymalna grubość
warstwy Podkładu podłogowego 8.0 powinna wynosić
60 mm.
W przypadku Posadzki cementowej 8.1 oraz Betonit B25 8.6
minimalna grubość warstwy powinna wynosić:
# 15 mm – w przypadku podkładów związanych z podłożem,
# 30 mm – dla podkładów na warstwie oddzielającej,
# 45 mm – w przypadku podkładów pływających,
# 40 mm nad przewodami grzewczymi – w przypadku podkładu
z ogrzewaniem wodnym.
Z kolei maksymalna grubość warstwy dla obu produktów to
80 mm.
Powierzchnia dobrze wykonanego podkładu podłogowego
powinna być pozbawiona raków, pęknięć i ubytków. Powinna
być również czysta i odpylona. Równość podkładu sprawdza
się za pomocą 2-metrowej łaty, którą przykłada się w dowolnych
miejscach i kierunkach. Wszelkie odchylenia w postaci
prześwitów pomiędzy łatą a powierzchnią podkładu nie powinny
być większe niż 5 mm. Należy je mierzyć z dużą dokładnością.
Odchylenie powierzchni podkładu od płaszczyzny
nie powinno przekraczać 2 mm na 1 m i 5 mm na całej
długości lub szerokości pomieszczenia.
Układanie okładzin na podkładzie może być wykonywane
po upływie 4 tygodni od jego wykonania oraz gdy jego
wilgotność nie przekracza 2%, a w przypadku parkietów
i paneli 1,5%.
W przypadku podłóg ogrzewanych do przyklejania płytek
ceramicznych można przystąpić dopiero po przeprowadzeniu
tzw. wygrzewania podkładu. Proces ten polega na
cyklicznym zwiększaniu i zmniejszaniu temperatury ogrzewania
podłogowego. Zabieg ten jest niezbędny – zapobiega
nagłemu odparowaniu wody zawartej w podkładzie podłogowym.
Pominięcie wygrzewania podkładu może skutkować
jego spękaniem, odspajaniem się płytek od wylewki
a w skrajnych przypadkach pojawianiu się spękań również
na powierzchni płytkach ceramicznych. W pierwszym dniu
wygrzewania podnosi się temperaturę ogrzewania podłogowego
o 5oC w stosunku do temperatury otoczenia. Nagrzewanie
w kolejnych dniach odbywa się poprzez podwyższanie
temperatury o kolejne 5°C dziennie, aż do osiągnięcia maksymalnej
temperatury ogrzewania podłogowego 50°C. Taką
temperaturę utrzymuje się krótko, maksymalnie jedną dobę.
W kolejnych dniach obniża się temperaturę w instalacji
o 5°C dziennie, aż podkład osiągnie temperaturę wyjściową.
Do przyklejania płytek na ogrzewanej wylewce należy stosować
klej o podwyższonej odkształcalności (tzw. klej elastyczny),
np. Zaprawę klejącą Gabit Super 7.1. Przed przystąpieniem
do przyklejania płytek podłoże trzeba oczyścić z kurzu,
tłuszczów i innych substancji obniżających w znacznym
stopniu przyczepność. Podłoże wymaga też zagruntowania.
W tym celu sprawdzi się Grunt Akrylowy Głębokopenetrujący
9.7 SOLBET.